Novenco PTFE Rods
NOVENCO produces PTFE Rods and Tubes in a wide range of sizes, colors, and PTFE materials.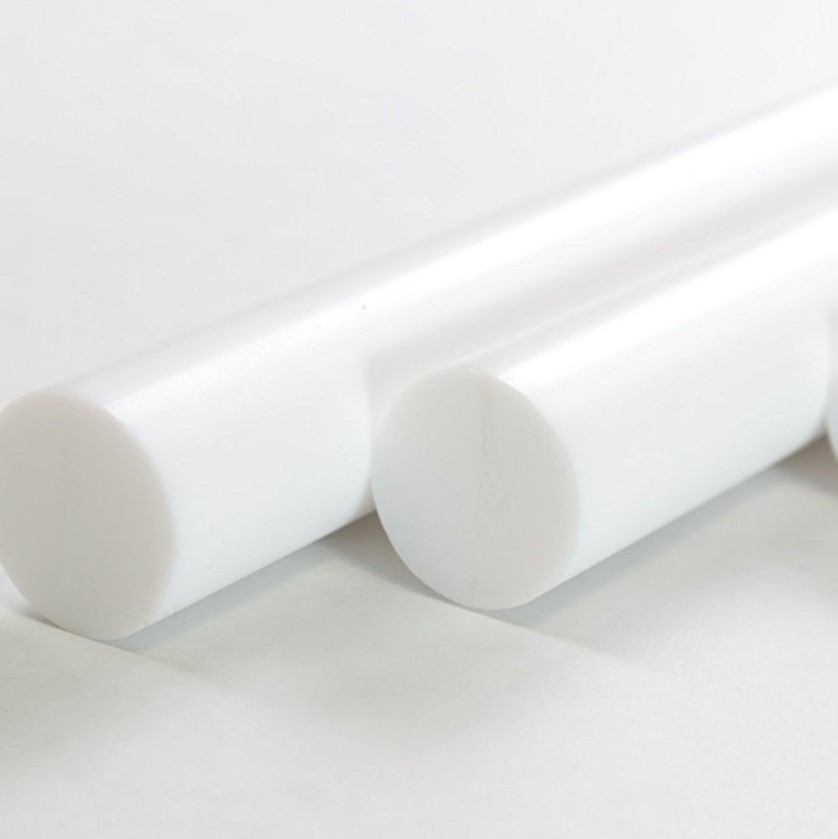
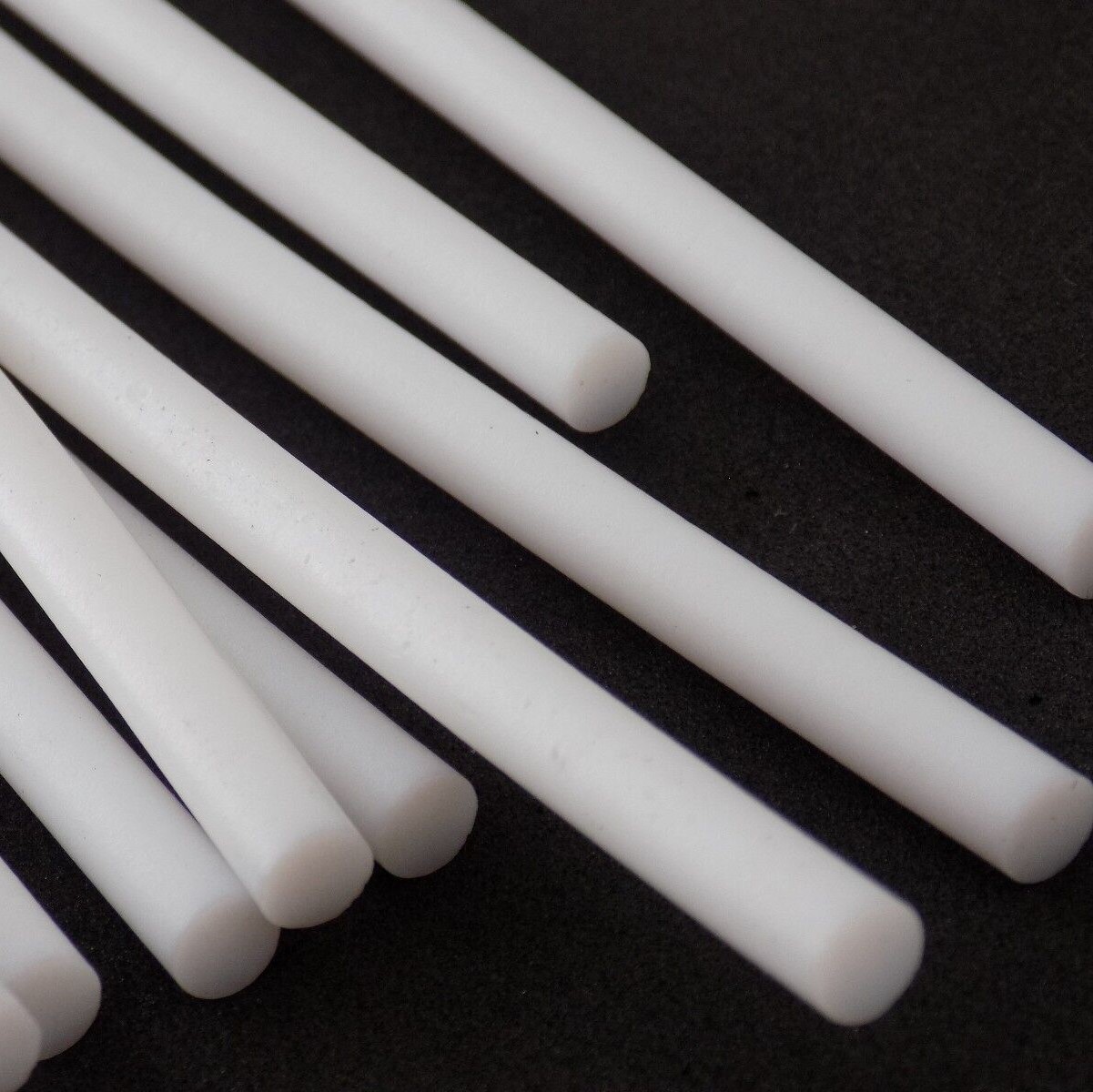
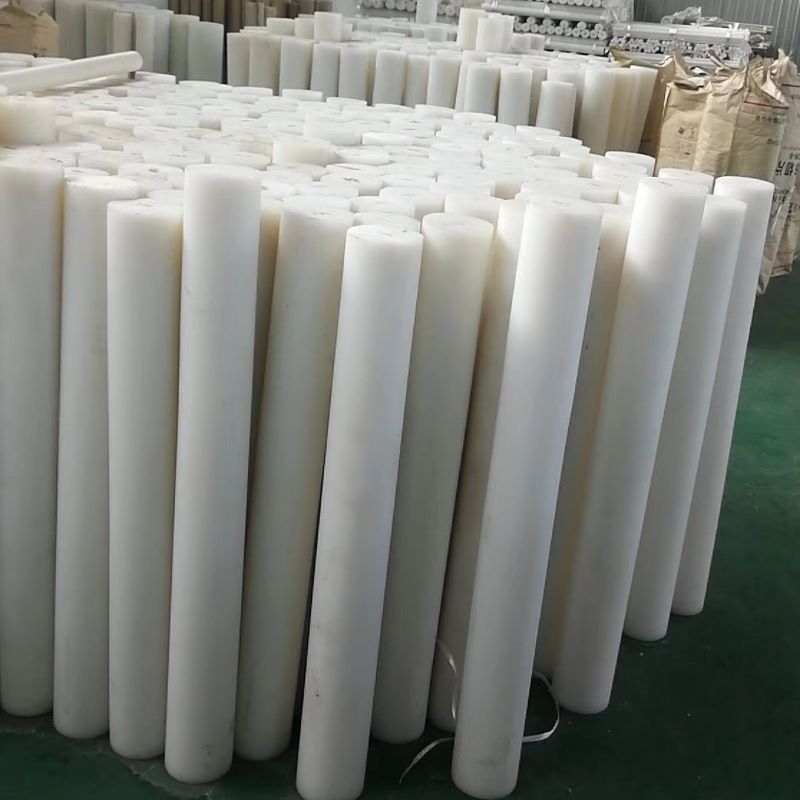
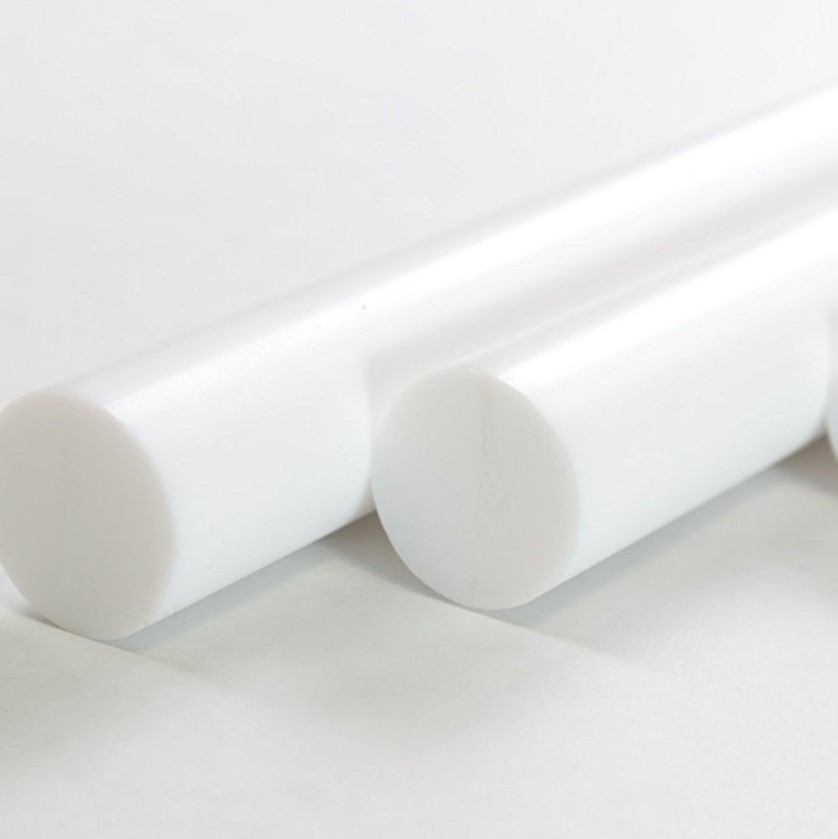
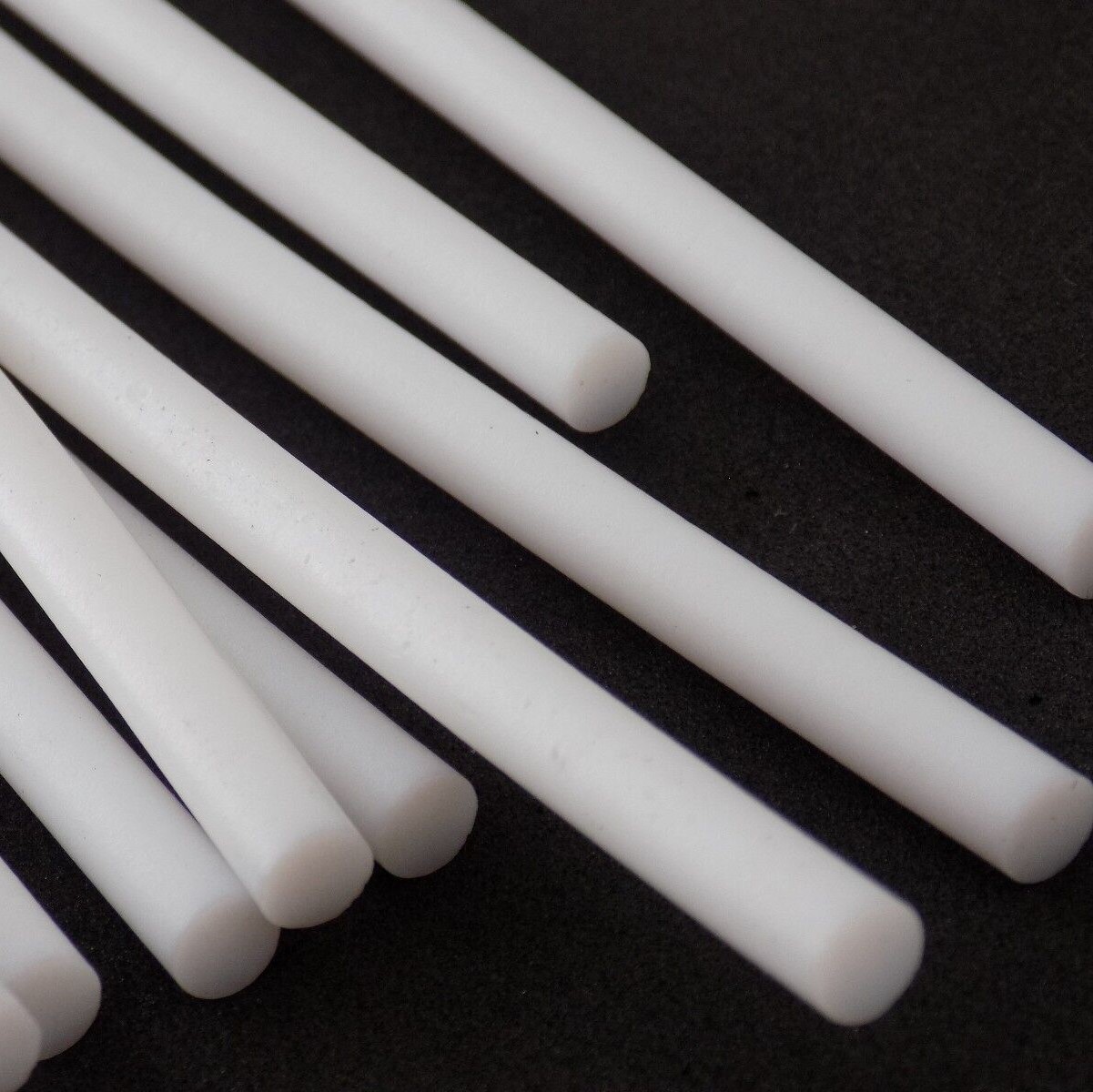
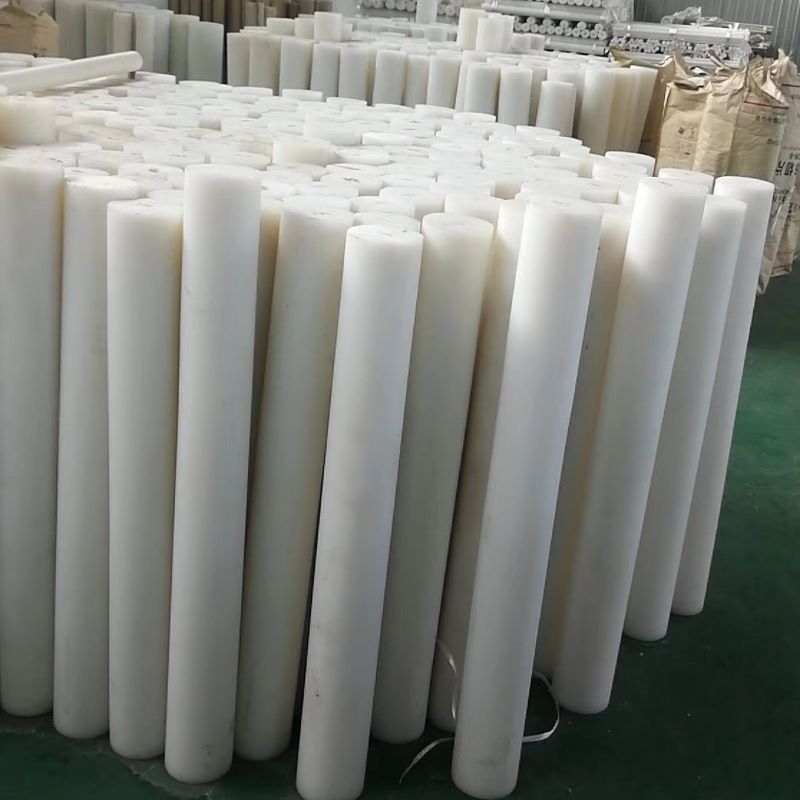
PTFE RODS & TUBES
NOVENCO produces PTFE Rods and Tubes in a wide range of sizes, colors, and PTFE materials (Poly tetra fluoro ethylene), including our NEC 12 Rod or Tube is a low friction product that is inert to most liquids and corrosives, and is also noncontaminating, making it the perfect material for use in applications where metals and alloys would corrode quickly. Capable of withstanding temperatures from 328°F up to +500°F. NEC 12 can handle a vast range of environments and is thus, used regularly in high temperature applications.
While NEC 12 Rods and Tubes are mostly white in color, they can also be made from blended materials to meet customer application requirements. Adding a filler will generally color the Rod or Tube to match the filler, but other custom colors can also be obtained. However, custom colors must be requested prior to fabrication. Certain fillers or colors may affect the physical properties of the material. Please inform us if testing of a certain blend is required.
NOVENCO stocks a wide range of molded and extruded tubes and rods, in virgin PTFE + Recycled PTFE as well as blended compounds which help us to ensure fast and efficient service. We usually stock rod made of a combination of virgin PTFE + Recycled PTFE.
Properties | Unit | Method | Typical Value |
---|---|---|---|
PHYSICAL-MECHANICAL | |||
Density | g/cm3 | ASTM D792 | 2.14 - 2.18 |
Hardness - Shore D | points | ASTM D2240 | 51 - 60 |
Tensile strength - CD | Mpa | ISO 527 | ≥ 20 |
Elongation at break - CD | % | ISO 527 | > 200 |
Compressive Strength at 1% deformation- CD | psi | ASTM D695 | 580 - 725 |
Deformation under load at room temperature after 24 hours at 13.7 N/mm2 - CD | % | ASTM D621 | 14-17 |
Deformation under load at room temperature after 24 hours at 13.7 N/mm2 - CD | % | ASTM D621 | 14-17 |
Permanent deformation as above after 24 hours of rest at room temperature- CD | % | ASTM D621 | 7 - 8 |
Deformation under load at 260oC,2 after 24 hours at 41 N/mm -CD | % | ASTM D621 | |
Permanent deformation as above after 24 hours of rest at room temperature-CD | % | ASTM D621 | 7 - 8 |
Impact strength lzod | J/m | ASTM D256 | 153 |
TRIBIOLOGICAL | |||
Dynamic coefficient of friction | / |
ASTM D1894 ASTM D3702 |
0.06 |
Wear factor K | / | ASTM D3702 | 2.900 |
PV limit
at 3 m/min
at 30 m/min at 300 m/min |
N/mm2.m/min | / |
2.4 4.2 5.7 |
THERMAL | |||
ServiceTemperature(min-max) | oF | / | -328 /+500 |
Thermal expansion coefficient (linear ) 25 -100oC | 10-5in/inoF | ASTM D696 | 6.625 - 7.206 |
ELECTRICAL | |||
Dielectric strength (specimen 0.5 mm thick) | KV/mm | ASTM D149 | ≥ 20 |
Dielectric Constant at 60 Hz and 106 Hz | / | ASTM D150 | 2.05 - 2.10 |
Volume Resistivity | Ω • cm | ASTM D257 | 1018 |
Surface Resistivity | Ω | ASTM D257 | 1017 |
Diameter (mm) | Tolerance (mm) | Length (mm) | Tolerance (mm) |
---|---|---|---|
4 | +0.3-0.3 | 305/1000/2000 | +20-0 |
5 | +0.3-0.3 | 305/1000/2000 | +20-0 |
6 | +0.3-0.3 | 305/1000/2000 | +20-0 |
8 | +0.4-0.4 | 305/1000/2000 | +20-0 |
10 | +0.4-0.4 | 305/1000/2000 | +20-0 |
12.5 | +0.8-0.8 | 305/1000/2000 | +20-0 |
15 | +0.8-0.8 | 305/1000/2000 | +20-0 |
18 | +0.8-0.8 | 305/1000/2000 | +20-0 |
20 | +0.8-0.8 | 305/1000/2000 | +20-0 |
25 | +1.2-1.2 | 305/1000/2000 | +20-0 |
28 | +1.2-1.2 | 305/1000/2000 | +20-0 |
30 | +1.6-1.6 | 305/1000/2000 | +20-0 |
32 | +1.6-1.6 | 305/1000/2000 | +20-0 |
35 | +1.6-1.6 | 305/1000/2000 | +20-0 |
38 | +2.0-2.0 | 305/1000/2000 | +20-0 |
40 | +2.0-2.0 | 305/1000/2000 | +20-0 |
45 | +2.0-2.0 | 305/1000/2000 | +20-0 |
50 | +2.0-2.0 | 305/1000/2000 | +20-0 |
55 | +2.6-2.6 | 305/1000/2000 | +20-0 |
60 | +2.6-2.6 | 305/1000/2000 | +20-0 |
65 | +2.8-2.8 | 305/1000/2000 | +20-0 |
70 | +2.8-2.8 | 305/1000/2000 | +20-0 |
75 | +3.2-3.2 | 305/1000/2000 | +20-0 |
80 | +3.2-3.2 | 305/1000/2000 | +20-0 |
Diameter (mm) | Tolerance (mm) | Length (mm) | Tolerance (mm) |
---|---|---|---|
85 | +3.6-3.6 | 305/1000/2000 | +20-0 |
90 | +3.6-3.6 | 305/1000/2000 | +20-0 |
95 | +3.6-3.6 | 305/1000/2000 | +20-0 |
100 | +4.0-4.0 | 305/1000/2000 | +20-0 |
105 | +4.0-4.0 | 305/1000/2000 | +20-0 |
110 | +4.0-4.0 | 305/1000/2000 | +20-0 |
115 | +4.0-4.0 | 305/1000/2000 | +20-0 |
120 | +5.0-4.0 | 305/1000/2000 | +20-0 |
125 | +5.0-4.0 | 305/1000/2000 | +20-0 |
130 | +5.0-4.0 | 305/1000/2000 | +20-0 |
135 | +5.0-4.0 | 305/1000/2000 | +20-0 |
140 | +5.0-4.0 | 305/1000/2000 | +20-0 |
145 | +5.0-4.0 | 305/1000/2000 | +20-0 |
150 | +5.0-4.0 | 305/1000/2000 | +20-0 |
160 | +5.0-4.0 | 305/1000/2000 | +20-0 |
170 | +5.0-4.0 | 305/1000/2000 | +20-0 |
180 | +5.0-4.0 | 305/1000/2000 | +20-0 |
190 | +5.0-4.0 | 305/1000/2000 | +20-0 |
200 | +6.0-3.0 | 305/1000/2000 | +20-0 |
210 | +6.0-3.0 | 305/1000/2000 | +20-0 |
220 | +6.0-3.0 | 305/1000/2000 | +20-0 |
230 | +6.0-3.0 | 305/1000/2000 | +20-0 |
240 | +6.0-3.0 | 305/1000/2000 | +20-0 |
250 | +6.0-3.0 | 305/1000/2000 | +20-0 |